A tensile test, also known as tension test, is probably the most fundamental type of mechanical test that can be performed on material to have an idea about the mechanical properties of the materials used in the structural design. Tensile tests are simple, relatively inexpensive, and fully standardized.
The main feature of tension test:
1- Preparation of tension test specimen.
2- The specimen may be of arbitrary cross sectional area depending on the standard used and the shape
of the tested material.
3- The cross section should be constant throughout the test length.
4- Load should increase gradually and axially till the failure occur.
Tension test is the simplest test which used to give an idea about the mechanical properties of the metal used in the structure design as the ferrous and nonferrous metals and alloys.
Data from tension test:
1. The proportionality limit σp
It is the greatest tensile stress at which the stress is proportional to the resulted strain.
The first part of the curve is a straight line which represent "HOOK'S LAW" till the point P … here the stress is proportional to the strain.
2. The elastic limit ( σE ) :-
It is the greatest tensile stress that a substance can withstand without permanent (plastic deformation). It is usually difficult to find this experimentally for which reason the 0.01 limit ( σ0.01) and the 0.005 limit considered as the elastic limit. In practice, therefore, the elastic limit is the stress due to which a plastic elongation of 0.01% or 0.005% takes place.
3. The upper yield point ( σyu ) :-
It is the maximum tensile stress at which plastic deformation occurs without increasing the deforming load. The load will increase with presence deformation in the metal.
4. The lower yield point (σyl ) :-
It is the min. tensile stress at which plastic deformation takes place without increasing of
load. It is explained by the presence of certain concentration of solute atoms of carbon
or nitrogen on the slip planes overcoming the resistance of glide on these plaines lead
to the presence of the higher and the lower yield points.
5. The tensile strength or ultimate strength σUTS :-
It is the greatest tensile strength without breaking the tensile strength: Ultimate strength

Loading up to the peak load (or ultimate tensile stress) the resulting elongation is uniform on the whole specimen length. After this point some instability features like forming of cracks, voids and other damage feature lead to concentrating the deformation in the region where the fracture will take place.
6. The break stress ( σB ) :-
It represents the stress at which the specimen breaks.
σB usually it is less practical than the tensile strength σUTS .
in the design of any structure neither the ultimate stress nor the brack stress would be taken into consideration. It is the yield stress with a safety factor that is near 1.5 to avoid the failure of the construction. Beside the above determined data from the tension test, the value of elongation and reduction of area estimated in a tension test are of great practical importance.
7. The elongation or percent elongation :-
It is a measure of the ductility or formability of metal and is represented by the given formula:


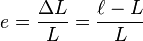
9. The reduction of area
is a measure of the ductility of the metal and is given in percent.
"R.A.": usually refers to the total reduction of the area before failure and if a neck is formed, the value of R.A. is determined by measuring the cross sectional area at the point where break occurs.

10. The toughness of a metal :-
The area under the stress-strain diagram is taken as a measure for the toughness of a metal.
11. The resilience of a metal :-
The area under (0, E) curve line is the resilience of the metal and could be defined as the work done by an elastic body to return to its initial shape.
Materials with high resilience are used to products subjected to different sudden loads such as spring material.
0 التعليقات:
Post a Comment